OBJECTIVE:
Set the custom parameters for an irregular shaped tank with a 600mm 30-240ohm KUS tank sender.
Cerbo GX.
QUESTION:
How does a user calculate with mathematical certainty the "Sensor Level" in % to calibrate a known volume in %?
EXAMPLE:
The photo attached show the set points that have been added for my particular installation to work correctly.
Take Note the sensor value at Point 1 is 52% and the volume is at 10% which corresponds to approximately 120mm of rise in the float at 100 Litres.
(I have calibrated all these values to work correctly by trial and error)
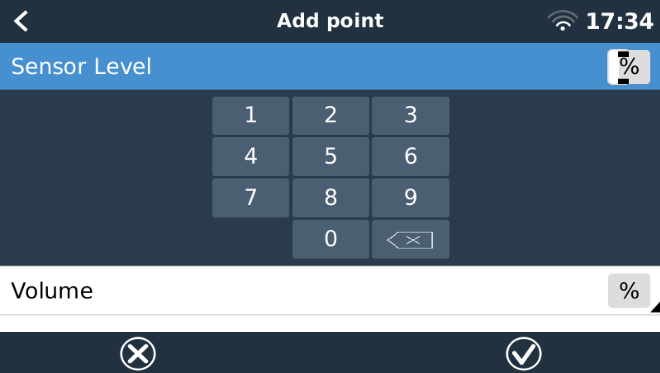
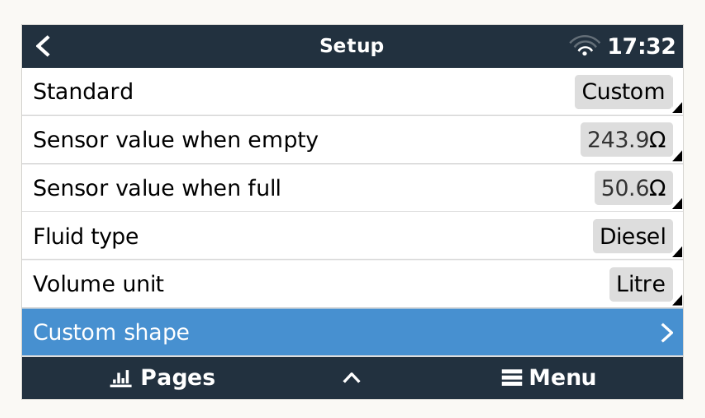